Classification of electroplating and the process flow of electroplating materials
Electrogalvanizing is the process of forming uniform, compact and well-bonded metal or alloy deposits on the surface of the parts by electrolysis.Compared with other metals, zinc is relatively cheap and easy to be coated a metal, is a low value corrosion protection electroplating, is widely used to protect steel parts, especially to prevent atmospheric corrosion, and used for decoration.Plating technology includes slot plating (or hanging plating), rolling plating (suitable for small parts), automatic plating and continuous plating (suitable for wire and strip).
1. Classification of electroplating
At present, according to the domestic electroplating solution classification, can be divided into four categories:
1. Cyanide zinc plating
Because (CN) is highly toxic, environmental protection has put forward strict restrictions on the use of cyanide in electroplating, and constantly promoted the development of the system of reducing cyanide and replacing cyanide electroplating solution, requiring the use of low-cyanide (micro-cyanide) electroplating solution.
After using this process, the product quality is good, especially color plating, after passivation, the color is kept good.
2. Zincate galvanizing
This process evolved from cyanide galvanizing.Currently, there are two major factions in China, namely:
A. "DPE" series of wuhan material protection institute;
B. "DE" series of the broadcasting institute.Both belong to the alkaline additive zincate zinc, with a PH of 12.5~13.
Using this process, the coating lattice structure is columnar, good corrosion resistance, suitable for color galvanized.
Note: after the product is out of the tank → washing → light (nitric acid + hydrochloric acid)→ washing → passivation → washing → washing → washing → scalding → drying → drying → aging treatment (in the oven at 80~90℃).
3. Chloride zinc plating
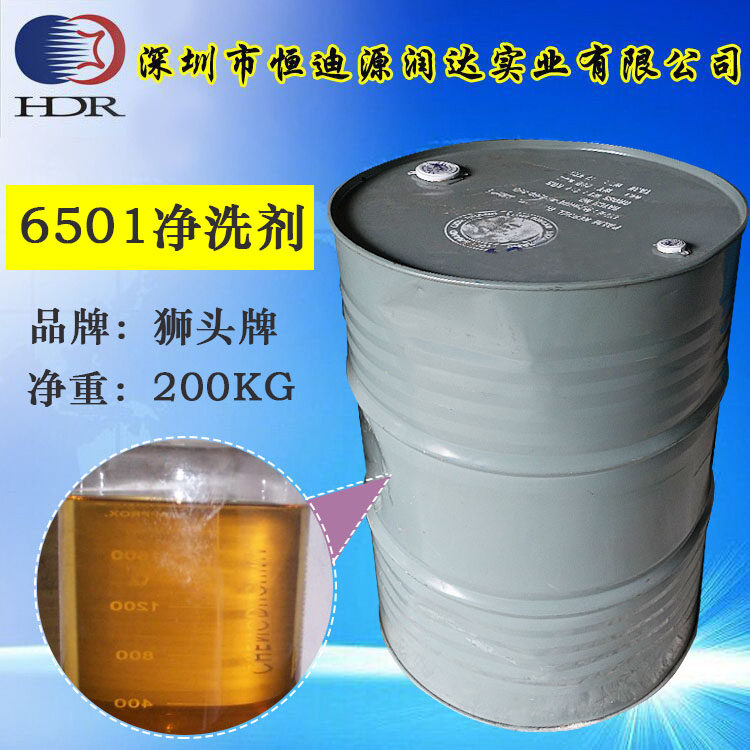
This process is widely used in the electroplating industry, accounting for up to 40%.
After passivation (blue white) can replace zinc chromium (and chrome plating), especially in addition to water soluble varnish, it is difficult for the layman to identify the zinc or chrome plating.
This process is suitable for white passivation (blue white, silver white).
4. Sulfate galvanization
This process is suitable for continuous plating (wire, strip, simple, coarse and large parts), low cost.
2. Electric galvanizing process
1. Electric galvanizing process
Taking galvanized iron alloy as an example, the process flow is as follows:
Chemical oil removal → hot water washing → water washing → electric oil removal → hot water washing → water washing → strong corrosion → water washing → electric galvanized iron alloy → water washing → water washing → light out → passivation → water washing → drying.
2. Preparation of electroplating bath
Preparation of plating solution (take lL as an example) :
(1) add 1/3 volume of pure water into the plating tank;
(2) dissolve sodium hydroxide with 1/3 pure water (it will generate heat when dissolved, so be careful);
(3) with a small amount of water to adjust the zinc oxide into a paste, and then add more pure water, full mixing.The stirred zinc oxide was slowly added to the dissolved sodium hydroxide solution and stirred while adding to make it fully complexed and then added to the plating tank.
(4) when the bath temperature drops below 30~C, add 85g Baser and stir thoroughly;
(5) dissolve 15mL BaseF in 15gBaseR, and then add the mixture into the plating tank;
(6) add 4mL h-o624 and stir well;Add water to desired volume;
(7) adding brighteners zf-105a and zf-105b;Stir well.
Black passivation process: washing → light → washing → black passivation → washing → post-treatment → drying.
3. Influencing factors of electric galvanizing
(1) influence of zinc content
Zinc content is too high, light range is narrow, easy to obtain thick coating, coating iron content is reduced;The zinc content is too low, the brightness range is wide, it takes a long time to reach the required thickness, the iron content in the coating is high.
(2) the influence of sodium hydroxide
Sodium hydroxide content is too high, high temperature operation is easy to scorch;When the content of sodium hydroxide is too low, the dispersibility is poor.
(3) the influence of iron content
The iron content is too high, the iron content in the coating is high, the passivation film is not bright;Low iron content, low iron content in the coating, corrosion resistance, olive color.
(4) the influence of brightener
Zf-iooa is too high, the coating is brittle;Too low, low current area no coating, passivation color is not uniform;ZF 1 100B is too high, the coating is brittle;Too low, the entire plating does not shine.
(5) the influence of temperature
The temperature is too high, the dispersion ability decreases, the iron content in the coating is high, the corrosion resistance decreases, the passivation film color is not uniform, hair flower;Temperature is too low, high current density area charred, coating brittleness, deposition speed is slow.
(6) the influence of cathode movement
Cathode movement must be used.Moving too fast, high current density area coating rough;Too slow, may produce airflow, local no coating.